Comprehending the Basics and Applications of Plastic Extrusion in Modern Production
In the world of modern manufacturing, the technique of plastic extrusion plays a crucial role. Untangling the fundamentals of this procedure discloses the true convenience and possibility of plastic extrusion.
The Basics of Plastic Extrusion Refine
While it may show up facility, the fundamentals of the plastic extrusion procedure are based upon reasonably straightforward concepts. It is a production procedure in which plastic is melted and after that shaped right into a constant account through a die. The raw plastic product, typically in the kind of pellets, is fed right into an extruder. Inside the extruder, the plastic is subjected to heat and pressure, causing it to thaw. The liquified plastic is then required through a shaped opening, referred to as a die, to form a long, continuous product. The extruded product is cooled and afterwards reduced to the preferred size. The plastic extrusion procedure is thoroughly made use of in different industries due to its cost-effectiveness, efficiency, and convenience.
Different Sorts Of Plastic Extrusion Strategies
Structure upon the basic understanding of the plastic extrusion process, it is essential to check out the numerous strategies entailed in this production approach. Both main techniques are profile extrusion and sheet extrusion. In profile extrusion, plastic is melted and developed into a constant account, typically made use of to produce pipes, rods, rails, and window structures. In contrast, sheet extrusion produces huge, level sheets of plastic, which are normally more processed right into items such as food product packaging, shower drapes, and automobile parts. Each strategy needs specialized machinery and exact control over temperature and stress to make sure the plastic keeps its shape during air conditioning. Comprehending these methods is key to making use of plastic extrusion successfully in modern manufacturing.
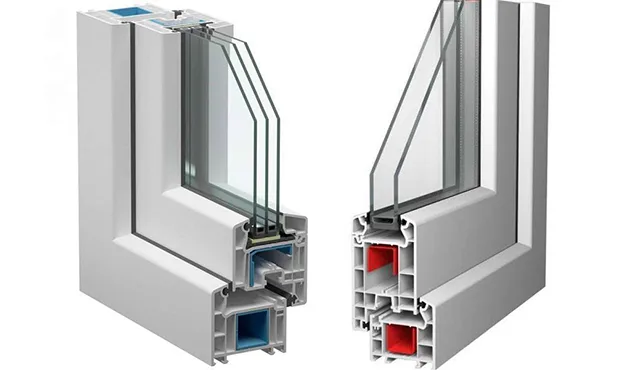
The Role of Plastic Extrusion in the Automotive Industry
An overwhelming majority of parts in modern-day vehicles are items of the plastic extrusion procedure. Plastic extrusion is mostly made use of in the manufacturing of different vehicle parts such as bumpers, grills, door panels, and control panel trim. Thus, plastic extrusion plays a pivotal duty in automotive production.
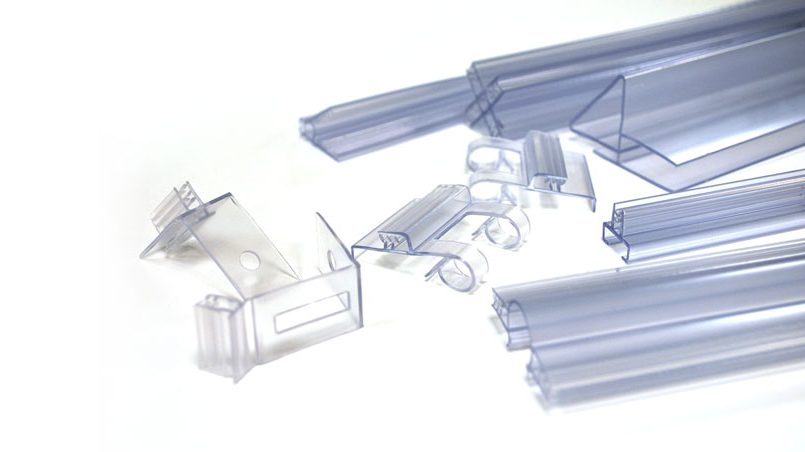
Applications of Plastic Extrusion in Durable Goods Manufacturing
Past its substantial effect on the auto sector, plastic extrusion confirms equally efficient in the realm of customer products producing. This process is important in creating a wide range of products, from food product packaging to house devices, playthings, and also medical devices. The adaptability of plastic extrusion permits makers to create and create complicated sizes and shapes with high precision and efficiency. In addition, as a result of the recyclability of numerous plastics, extruded elements can be reprocessed, reducing waste and expense. The adaptability, flexibility, and cost-effectiveness of plastic extrusion make it a preferred choice for several durable goods producers, contributing dramatically to the sector's development and development. The environmental implications of this prevalent usage require careful consideration, a subject to be discussed further in the succeeding section.
Environmental Influence and Sustainability in Plastic Extrusion
The prevalent use of plastic extrusion in manufacturing welcomes examination of its environmental ramifications. Effective equipment decreases energy use, a knockout post while waste management systems recycle scrap plastic, reducing raw material demands. Despite these improvements, additionally innovation is needed to reduce the environmental impact of plastic extrusion.
Conclusion
In verdict, plastic extrusion plays a crucial function in modern-day production, particularly in the vehicle and customer products sectors. Comprehending the basics of this procedure is crucial to enhancing its applications and advantages.

The plastic extrusion procedure is thoroughly made use of in different sectors due to its efficiency, versatility, and cost-effectiveness.
Structure upon the standard understanding of the plastic extrusion procedure, it is necessary to his comment is here check out the different techniques entailed in this production approach. plastic extrusion. In comparison, sheet official source extrusion produces big, flat sheets of plastic, which are usually further processed right into items such as food packaging, shower curtains, and cars and truck components.An overwhelming majority of parts in modern-day lorries are items of the plastic extrusion process